5 Common Mistakes to Avoid in PLC Programming for Industrial Automation
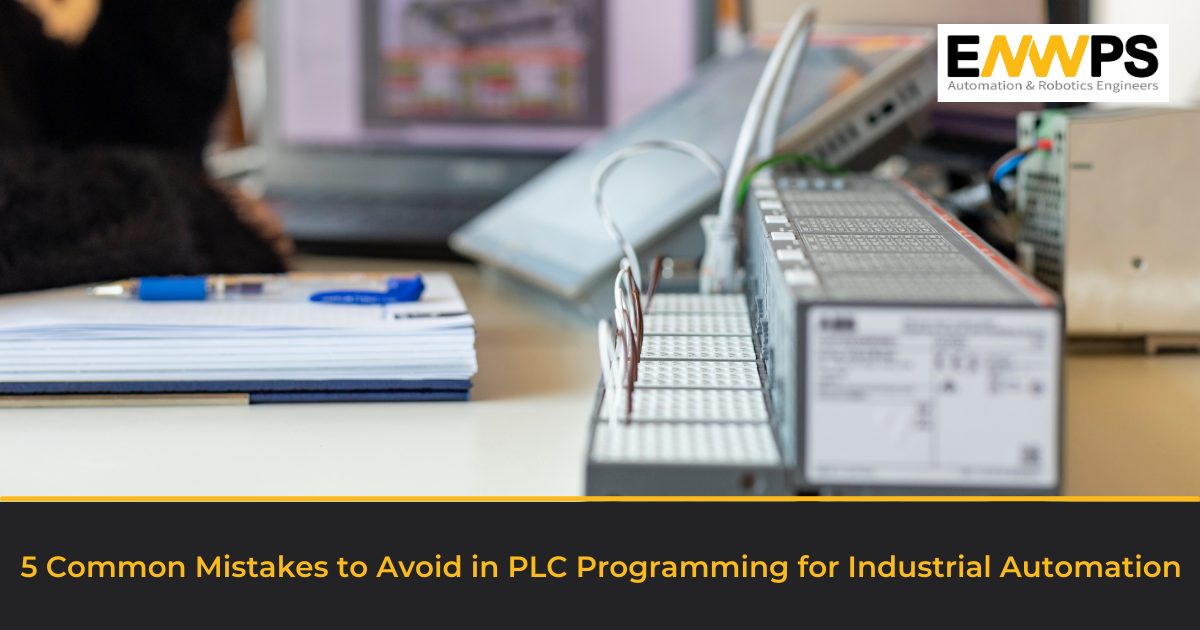
Programmable Logic Controllers (PLCs) have revolutionized the way industrial automation works by providing an efficient and reliable method of controlling machinery and processes. However, as with any technology, there are certain common mistakes that can occur when programming PLCs. These mistakes can lead to costly downtime, production losses, and even safety hazards. In this blog post, we will explore the top 5 common mistakes to avoid in PLC programming for industrial automation. By understanding these mistakes and how to prevent them, you can ensure that your automation systems run smoothly and efficiently, maximizing productivity, and minimizing downtime.
What is PLC Programming?
PLC programming is the process of creating software programs for Programmable Logic Controllers (PLCs), which are used to control and automate processes in manufacturing plants, production lines, and other industrial applications. PLC programming involves writing logic and algorithms using specialized programming languages or graphical interfaces to sense the inputs and control the outputs of the PLC, such as sensors, actuators, motors, and other devices. The programming is typically done by automation engineers or control system designers who have a deep understanding of the PLC’s hardware and software components, as well as the processes and systems that the PLC will be used to control. The goal of PLC programming is to create efficient and reliable automation systems that increase productivity, improve product quality, and enhance safety in industrial settings.
Here are the 5 common mistakes to avoid in PLC:
Mistake #1: Poor Planning
Poor planning can lead to inefficient programming practices, wasted time and resources, and ultimately, a system that doesn’t meet the intended requirements or specifications. Proper planning includes defining the system requirements and specifications, selecting the appropriate hardware and software components, creating a detailed program design, and establishing a testing and commissioning plan. Without proper planning, PLC programming can become disorganized and prone to errors. Therefore, it is essential to have a well-thought-out plan before starting any PLC programming project.
Mistake #2: Not Documenting Code
One of the most common mistakes in PLC programming is poor documentation of the code. Lack of documentation can make it difficult to maintain and troubleshoot the code in the future, and it can also make it harder for others to understand the program’s functionality. Proper documentation of the code, including comments, naming conventions, and clear logic, is essential for efficient and effective PLC programming.
Mistake #3: Ignoring Safety Requirements
Inadequate or ignored security measures in PLC programming can leave the system vulnerable to cyberattacks and other security threats. It’s important to implement proper security measures, such as password protection, firewalls, and encryption, to protect the system from unauthorized access and to ensure the integrity and confidentiality of data.
Mistake #4: Underestimating Debugging Time
Debugging is the process of identifying and correcting errors in the program code, and it is an essential part of PLC programming. However, debugging can be a time-consuming process, and programmers often underestimate the amount of time needed to debug their code. This can lead to delays in project completion and increased costs. To save time and resources in the long run debugging tools and techniques, such as simulation software or real-time monitoring, help make it more efficient.
Mistake #5: Neglecting Software Updates
Software updates are essential for maintaining the reliability, security, and performance of the PLC system. Updates often include bug fixes, security patches, and new features that can improve the functionality and efficiency of the system. Neglecting to install these updates can leave the system vulnerable to security threats, reduce performance, and limit the functionality of the system.
Conclusion
PLC programming is a crucial step for industrial automation. Most of the processes will be streamlined with the help of a well-planned and executed PLC program. Yes, the process makes the functioning easy and cost-efficient. However, if not taken these common mistakes into account, it might lead you to invest into extra resources and lose some of your precious time. So, next time when you are diving into the process, keep this blog handy and go with ENWPS to tick all the right boxes.
Talk to us today! Reach us on automation@enwps.com