The Role of PLC Programming in Predictive Maintenance and Equipment Monitoring
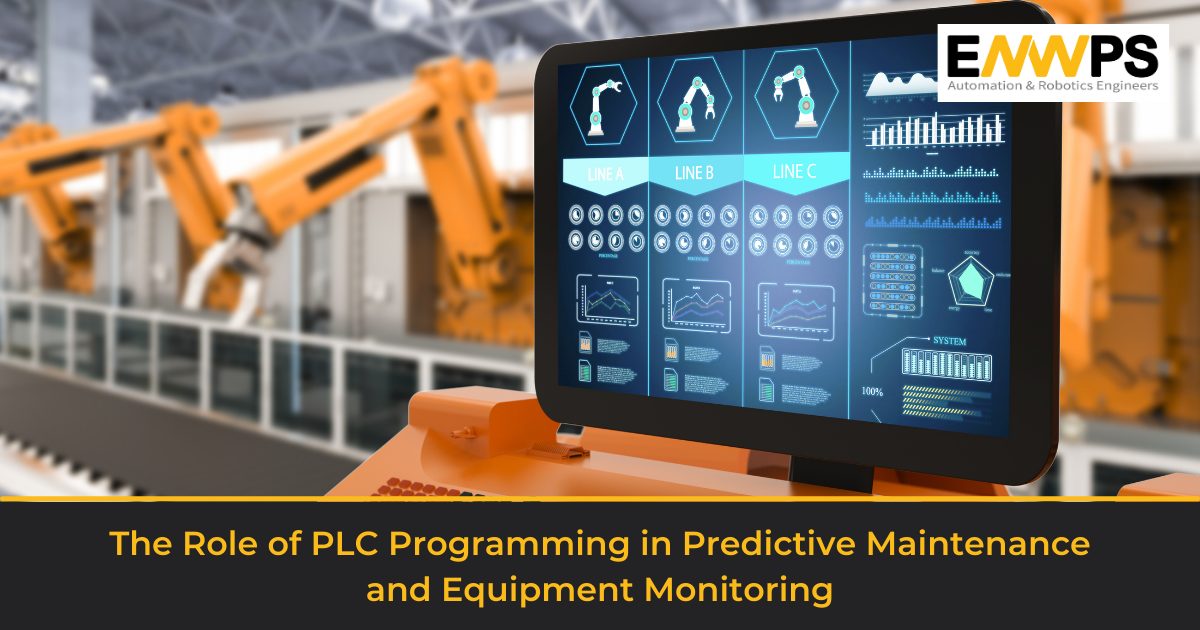
In the realm of industrial maintenance, staying ahead of equipment failures is crucial for minimizing downtime, reducing costs, and maximizing operational efficiency. One powerful tool that plays a pivotal role in achieving this proactive approach is PLC programming. By leveraging the capabilities of Programmable Logic Controllers (PLCs), manufacturers can implement predictive maintenance strategies and effectively monitor equipment health in real-time. In this article, we will explore the vital role of PLC programming in predictive maintenance and equipment monitoring. By using advanced technologies such as Programmable Logic Controllers (PLCs), manufacturers can improve their maintenance processes and increase their overall efficiency.
Also read our blog about: PLC in Predictive Maintenance: From Point Monitoring to Process Control
Overview of Predictive Maintenance and Equipment Monitoring
Predictive maintenance involves using data and analytics to predict when equipment is likely to fail, allowing for proactive maintenance to be performed before problems occur. Equipment monitoring, on the other hand, involves tracking the performance of equipment in real-time to identify potential issues before they become major problems.
Role of Programmable Logic Controllers in Predictive Maintenance
PLCs play a crucial role in predictive maintenance by providing a flexible and reliable platform for monitoring equipment and collecting data. By programming a PLC to monitor key performance indicators such as vibration, temperature, and pressure, manufacturers can detect potential issues before they become major problems.
How PLC Programming Improves Equipment Monitoring?
PLC programming can improve equipment monitoring by providing real-time data on the performance of equipment. This data can be used to identify trends and patterns that may indicate potential issues. By analyzing this data, manufacturers can make informed decisions about when to perform maintenance and what actions to take.
Real-Life Examples of Successful PLC Programs in Predictive Maintenance
There are many examples of companies that have successfully implemented PLC programs for predictive maintenance. For instance, one company used an inline or DIN-rail-mounted vibration transmitter to convert the output of a general-purpose ICP accelerometer into a 4-20 mA output compatible with a PLC. The PLC then sent alarms to the vibration analyst when vibration levels became excessive, alerting the predictive maintenance team of the need for closer investigation.
Potential Hurdles to Successful Implementation of PLC Programming for Predictive Maintenance
While PLC makes maintenance easy and increases overall efficiency, there are some points to consider to avoid stopping unexpected halts in the processes. Here are some potential hurdles to look for:
- Categorizing unpredictable tasks and applying predictive technology aptly.
- Effectively using the implemented technology.
- Neglecting the human factors associated with the changed/updated technology.
- Improper or no analysis of the collected data through the PLCs.
- Investing into predictive analytics software or an analytical team for timely analysis.
- Integrating data using various tools and techniques.
Future of PLC Programming in Equipment Monitoring
The future of PLC programming in equipment monitoring holds immense potential for revolutionizing maintenance practices in industrial settings. As technology continues to advance, PLC programming is set to become even more sophisticated and capable. Integration with advanced sensors, Internet of Things (IoT) devices, and data analytics platforms will enable PLCs to gather vast amounts of real-time equipment data. This data, coupled with advanced algorithms and machine learning techniques, will empower PLC programming to detect patterns, identify anomalies, and predict equipment failures before they occur.
The future of PLC programming in equipment monitoring envisions a proactive and intelligent maintenance approach, where PLCs autonomously monitor equipment health, provide actionable insights, and optimize maintenance schedules. By embracing these advancements, manufacturers can optimize asset performance, minimize downtime, and achieve higher operational efficiency in their industrial processes.
Predictions for the Growth and Advancements in this Field
As technology continues to advance, it is likely that we will see continued growth and advancements in the field of PLC programming for predictive maintenance and equipment monitoring. Manufacturers who invest in this technology will be well-positioned to improve their efficiency and competitiveness.
Conclusion
In conclusion, PLC programming plays an essential role in predictive maintenance and equipment monitoring. By implementing well-designed PLC programs, manufacturers can improve their maintenance processes, reduce downtime, and increase their overall efficiency.
Talk to us today! Reach us on automation@enwps.com