PLC in Predictive Maintenance: From Point Monitoring to Process Control
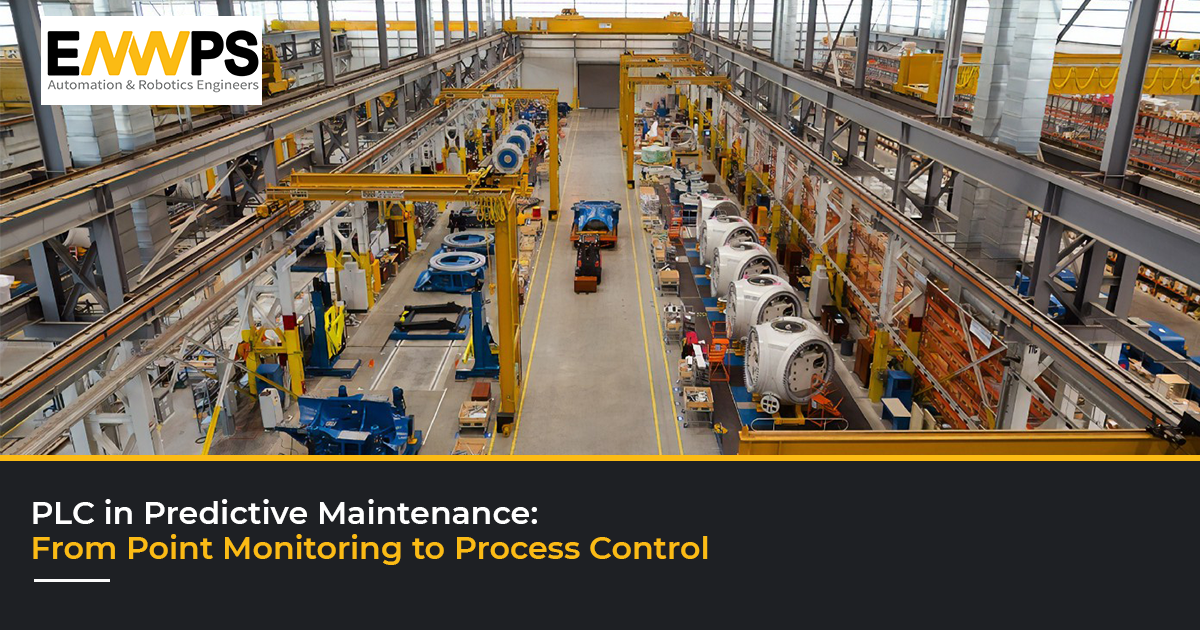
The modern PLC can be used to put in place a robust preventive maintenance programme.
What is a PLC?
A Programmable Logic Controller (PLC) is a type of computer used for machine control and is like the brain of a machine and holds the key for troubleshooting in case of any problem. PLC programming is done for specific tasks, so reviewing the steps in the program can lead to fault diagnoses and rectification. The PLC receives inputs from various sensors, switches, barcodes and other data fed by the operator, and gives output in the form of signals for the operation of motors, solenoids, indicators and alarms, etc., in a given sequence. Any change in the operation is effected through a PLC. Similarly any malfunction can be detected by reviewing the PLC actions. Now this is typical reactive maintenance once a fault occurs. Contemporary technologies go beyond that and in conjunction with IIoT devices and data analysis, a PLC can be used for predictive maintenance by anticipating faults and problem before they occur, analysing data patterns for anomalies and oddities.
How Data Acquisition Works in PLCs
For predictive maintenance, the PLC needs to use data, which is collected in course of the plant operation – data of parameters like vibration, temperature, electrical current, voltage, sound frequencies, pressure, etc., is collected by various sensors and dated, labelled and stored appropriately. While this data is good enough for regular troubleshooting, it is not enough for applications like preventive maintenance or other IIoT projects. The PLCs normally are programmed to measure parameters to indicate OK or Not OK, but not to monitor variations within those limits. This is because the primary role of a PLC is to control the machine operations and not data collection which is incidental. If any change has to be made in PLC operation, it needs a skilled programmer who may not be available and any attempt to do so without the expertise could actually have negative consequences. There are other methods of data acquisition but even those are not perfect.
So how can the data requirements for predictive maintenance be adequately addressed when it comes to PLCs? The answer here is provided by advances in technology, especially the IoT and Edge Computing devices that are now available for use with modern PLCs. These facilitate data collection from all the equipment (OT data) besides having the capability to process it further to provide structured data for storage in the cloud, also matching it with the requirements of the IT systems, offering transparency as well as greater control with better security through IT and OT collaboration. Modern PLCs also work with cloud platforms like Microsoft Azure or Amazon Web Services that make data collection and storage easier and provide tools to customise predictive maintenance operations as required.
Role of PLCs in Process Control & Monitoring
Plants exist to manufacture products, but the primary purpose of a plant is to make profit, which can be done only if the plant operates with optimum efficiency and minimum or no downtime. Any disruption in plant operation results in losses so process control and monitoring is extremely important, which brings the ball back to the PLC court. PLC, as mentioned earlier, is the brain of the machines and equipment, and is programmed to automatically control the operating conditions of the plant in which products are manufactured. Any deviation from process, in the absence of effective control, is likely to cause stoppage or worse, damage. Given the fact that most manufacturing processes are operating in harsh and hazardous environments, especially the chemicals or petrochemicals sectors, the smallest errors in reading of can cause significant safety problems and may even result in extensive damage to equipment or even loss of life. The role of a PLC in process control is thus central to safe plant operation with a predictive maintenance schedule in place.
Conclusion – How PLCs Ensure Smooth Plant Operation
A PLC is programmed to operate in a sequence and repeat the same in cycles. It can detect the status of each equipment operated with the output, and also monitor all input devices like sensors and switches in real time. It applies the user-created logic, and then executes it based on the input status, thereby controlling the devices like motors and valves, either turning them on or off. During these steps, the PLC also does a safety check by communicating with internal diagnostics and programming terminals, to ensure that everything is within normal operating conditions. Equipped with IIoT enabled data acquisition and analytics, the PLC acts quickly when a discrepancy occurs by alerting the operator, based on the built-in troubleshooting tools, initiating remedial measures. The modern PLC can be used to put in place a robust preventive maintenance program, avoiding costly downtime due to equipment failure.
ENWPS has been in business for 20 years and we specialize in Automation and Robotics. We provide innovative automated systems coupled with technology expertise. Our team of engineers, technicians and programmers design and develop customized solutions for a variety of end-user industries, including: Petrochemical, Manufacturing, Food and Beverage, and Pharmaceutical. Talk to us today! Reach us on rfq@enwps.com.