Design Considerations and Tips for Developing an Efficient HMI System
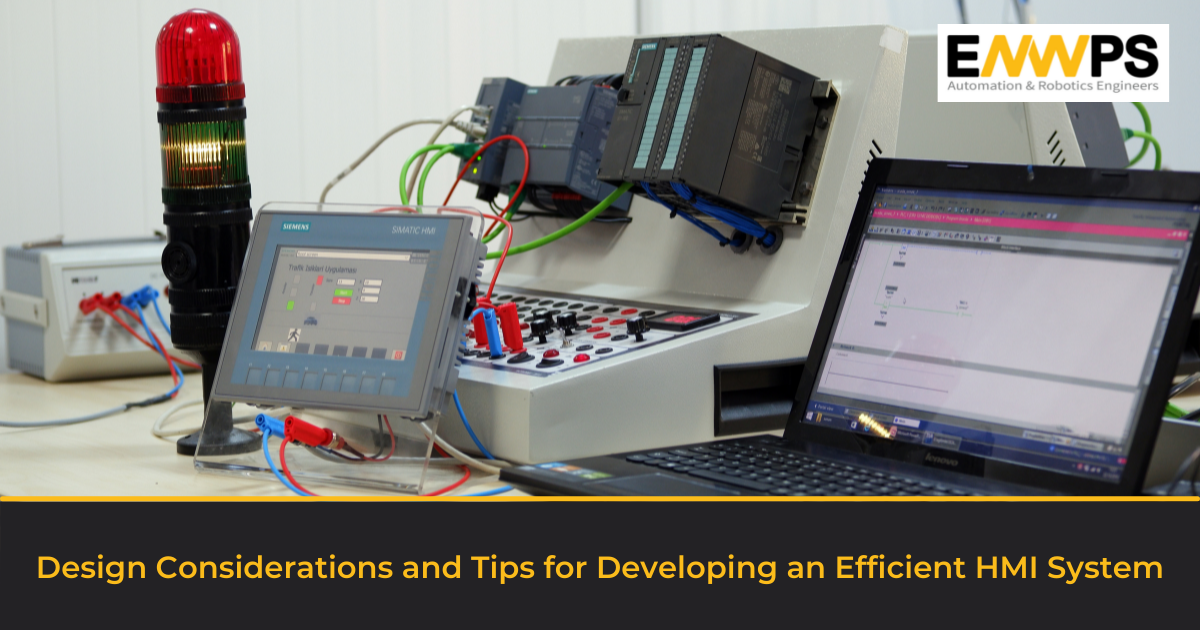
The HMI or Human-Machine Interface (HMI) evolved in the 1950s as a user interface that connects a person to a machine, when batch processing was the dominant mode of engaging with machines. At the most basic level, the HMI helps a user to interact with machines, most commonly in industrial processes or transportation systems like train and aircraft movements. It helps check the various parameters, displays the readings and generates alarms when these are exceeded. The evolution of the HMIs continues in the digital era with more and more features added, but the basic purpose remains the same – to provide insights into the performance and running conditions of machines and processes.
Importance of design in HMI
The HMI is what connects the machine or process with the human operator and hence performs a critical role in the smooth functioning of the machine or plant. It must provide, at a glance, all the critical parameters and functions of the machine in appropriate sequence and color codes to indicate critical parameters. A machine or process may have hundreds of functions, but not all are critical for safe running, so it is important to get the operator’s perspective when designing the HMI. At the same time it must also factor in the critical requirements of the process or operation and ensure the HMI serves the purpose for which it is designed. Above all, the HMI should be rugged to withstand the operating environment and last the life cycle of the equipment it controls.
How to design an HMI system?
Any device used for a critical function – the HMI falls in this category – must follow the standards prescribed for such devices in terms of design, layout, ergonomics, safety, and quality. One must also consider matters like the size of the HMI, the environmental conditions it will be exposed to, the materials of construction, IP ratings, etc., during the initial design process. Since the HMI is all about process parameters and machine health, it is important to capture all information and have adequate space for all the information that an operator must have access to, as well as presentation in appropriate format in terms of graphics, pie charts, tables, etc. It should not only indicate parameters and highlight abnormalities, but also generate alarms, and more importantly, log them. The HMI should also have the capability to interact with other devices, and above all, should be password protected to prevent unauthorized access.
Design considerations and tips
Since there is no one size fits all in matters of HMI selection, there are several important considerations when it comes to designing an HMI for a given application.
Here are the important considerations and tips:
- General functionality: What are the tasks that will be performed by the HMI? What type of actuation modes are required to initiate action – switches, pushbuttons, etc., and whether multiple functions can be combined, the number of screens, among other things; as also the modes and methods of feedback – auditory, visual or sensory.
- Defining the objectives: The short listing of the HMI design requirements begins by first determining the objectives. What is the equipment or process that is to be monitored, what are the controls to be vested with the operator, and what are the overall requirements of the HMI in the process.
- Functions and controls: The next step is to decide on the number of functions to be monitored and controlled and on the exact manner in which it is to be done – the number of screen displays, and the method of intervention by pushbuttons or rotary switches, the nature of feedback – audio, visual or vibratory.
- Degree of Input Complexity: It is important to decide the input mode – whether an On/Off switch or a sophisticated touchscreen display. Though touchscreen based HMI systems are preferred today, these are not suitable for all operating environments, especially in process industries. However, in certain applications, touchscreen operations are highly desirable, especially where there are many different controls in the process.
- Operator Feedback: What is the feedback mode to the operator? This is critical – the feedback can be audio, visual or sensory, or a combination of all three. Feedback is an essential feature of an HMI since it is a confirmation of the actions performed or a call for action, and should be compatible with the input mode as well.
- Interface/Interconnection with Other Systems: Since the HMI works in a manufacturing or process set up, it must be able to interface and connect with other devices for input or output like I/O points or serial bus. The HMI could also be networked with the MES system or in case of service industry, into the overall operations of the institution.
- Environmental Considerations: The physical location of the HMI in a particular environment is an important design consideration as it could be exposed to heat, moisture, vibrations, wear and tear and even deliberate abuse by vandals. Whether the factory floor or process industry environment, indoors or outdoors, environmental considerations must be factored in.
- Lifecycle Durability: Apart from environmental considerations, the HMI must be basically a sturdy unit to last as much as the equipment it is connected to, or its lifecycle. Failure of the HMI may cast a doubt on the entire equipment of the shop floor or the system.
- Style: While in a typical industrial environment, style may not matter much, but an item designed aesthetically always creates a positive impact. In case of a service industry like luxury hotels and public utilities, style becomes a significant design element.
- Regulatory/Standards Considerations: All industries are guided by certain engineering standards and regulatory considerations in terms of safety, durability and the operating environment. These could be standards and specifications as mandated by bodies like ANSI, IEC, IEEE or other industry specific standards for Oil & Gas and mining industries and even military grades, which the HMIs have to adhere to.
- Define the Operator: Notwithstanding the sophistication of the HMI, the operator is an important link in the system. The HMI must be designed with the operator in mind, and skill levels. There are routine systems that need operators with just basic skills and there are critical systems where the operators also function as troubleshooters. The HMI design should ideally consider the operator skills and for what functions it is used.
- Operators: Regardless of the profile and skills, the basic function of the HMI is to provide the operator access to the various controls for running the equipment for routine tasks, with information made available on request. The idea is to provide information for decision making, but at the same time reduce the possibilities to make errors.
- Supervisors: Apart from the operator, the HMI is also used by the supervisor, who has a greater control on the operations and may have a different login access for that. Some HMIs may even have different screens and more control options.
- Maintenance: There is yet another category who has even more access to the HMI functions than operators and supervisors and that is the maintenance personnel. So the HMI design must consider these distinctions and that should reflect in the design, layout, components, the screen presentation as well as safety aspects.
- Panel Layout: One of the critical design aspects of the HMI is the panel layout which should display the information in a manner consistent with the operation sequence and for intuitive access. The operator must also receive the feedback on the actions initiated, with timely prompts for further actions. The design of the HMI should also consider the use of appropriate accessories like buttons and switches. The Emergency Stop button must be prominently displayed and should not be prone to accidental activation.
- HMI Component Selection: The component selection for the HMI should be guided by practical considerations like the application requirements and how best are they suited in terms of electrical rating and safety, type of actuation – on-off/rotary, type of mounting, with/without pilot illumination, and the ability to withstand the operating environment.
- Color Scheme: Colors provide options, other than the traditionally used Green for Start, Red for Stop and Amber or Yellow for warnings. While colors used must be bright, the HMI should ideally avoid the use of too many colors or flashy displays as that could be distracting. The color should supplement the information rather than be the only source of it.
- Information Presentation: This is the main purpose of the HMI and it should be presented in as simple a manner as possible. There is no point in cluttering the display with too many data points as that could confuse the operator and cause errors and erratic responses. Clearly defined menus, use of graphics and separate screens for different sets of information may be considered.
- User Feedback: Finally, the crux of the matter – getting the feedback instantly for the actions initiated from the HMI. The operator should receive the feedback for every action initiated through the HMI in auditory or visual form or illuminated LED or switch to indicate the system status. It can also be a combination of signals mentioned above.
How can ENWPS assist in HMI selection?
With the advent of many different resources and components, designing a UI/HMI is not nearly as difficult as it used to be. But what matters is putting together an ideal device that suits the application perfectly. This is where experience matters.
ENWPS has experience of a quarter of a century in the field of automation and robotics, offering countless solutions to leading enterprises in India and abroad. This includes installation, programming and commissioning with complete project management capabilities in controls, electrical and mechanical engineering, PLC programming, HMI/SCADA configuration, etc. The company has the expertise to get down to the brass tacks of any project requirement, and arrive at the exact requirements for the HMI for a given application. It can handle it as a turnkey project, or help execute it, sourcing all the aggregates required.
Conclusion
As the interface between human and machine, the HMI performs a crucial role in running the equipment or a process. An off-the-shelf unit may not serve the purpose and getting a customized HMI that meets all the requirements of a particular machine or process is not easy. In such a case, professional expertise is of great help that will greatly reduce the pain points. Professionals at ENWPS can help here with all the expertise from advising on the right design to sourcing all the components, or simply custom-design one on a turnkey basis.
For more information or assistance, send us an email at rfq@enwps.com.