Everything You Need to Know About Robotics in Manufacturing
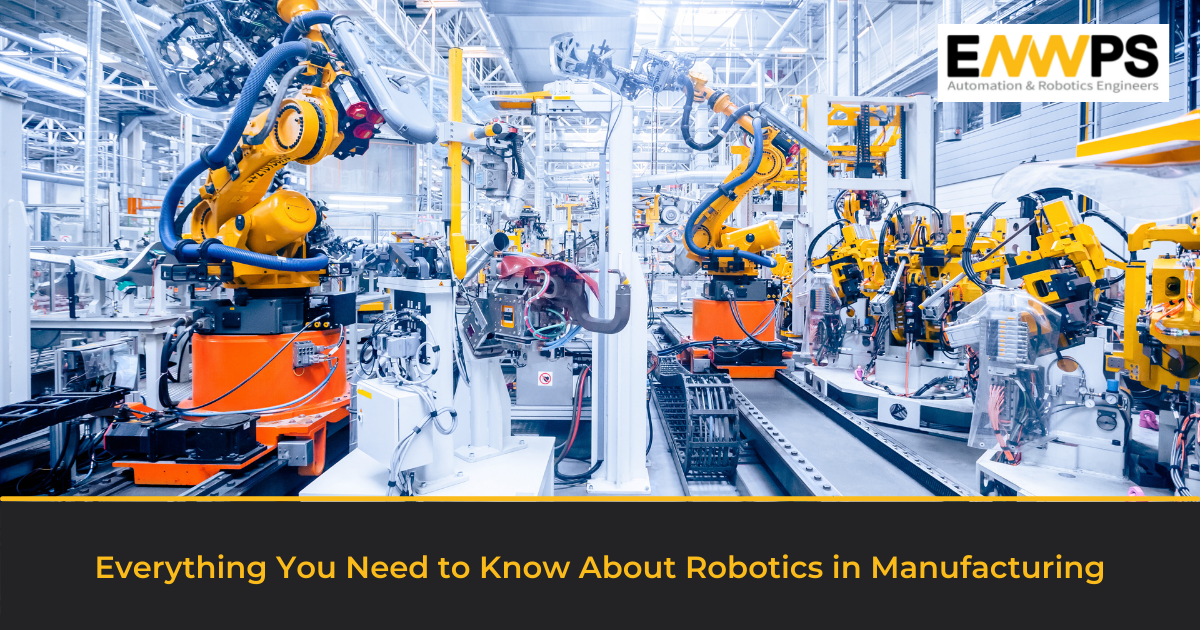
The term ‘robot’ is derived from Slavic roots denoting labour and was first used in 1920 by Czech writer Karel Čapek in a play about a factory fabricating artificial humans. Even before that, human beings were fascinated with the idea of some kind of automaton, which could do laborious jobs. Leonardo da Vinci’s Mechanical Knight from the Renaissance period was perhaps the best representation of this effort. It is not known whether da Vinci actually made a prototype, but a model constructed much later based on his design was found to be working with a combination of levers and pulleys.
The first modern programmable robot – a mechanical arm – was designed and manufactured by George Devol. Called the Unimate, Devol worked to refine this further with Joseph Engelberger, his contemporary and fellow inventor, who is today acknowledged as the ‘Father of Robotics’. The Unimate was an autonomous, pre-programmed robot designed to perform a task repeatedly. It was first installed in 1961 by General Motors at its factory to move pieces of hot metal. Thus began the evolution of the modern industrial robot.
Robotics in Manufacturing
Robots are ruling the manufacturing sector in the developed world. According to the latest sales figures released by the International Federation of Robotics (IFR), the operational stock of industrial robots hit a new record of about 3 million units worldwide – increasing by 13% on average each year (2015-2020). The report also mentions 5 key trends that are shaping robotics and automation around the globe, and the top trend is that segments that are relatively new to automation are rapidly adopting robots. The fact of the matter is, in a globalized world where nations are competing in exports of manufactured goods and trade surpluses, robots are playing an important role in productivity and economies of scale. There is no single factor behind the increasing adoption of robots in manufacturing. The most common advantages of robots over their human counterparts are by now too well known – speed, precision and accuracy, besides the ability to operate in hazardous locations. Robots do not get tired, do not make mistakes and do not report sick or need vacations. Together, these attributes have worked well in increasing production efficiency manifold, while at the same time reducing costs significantly.
A Brief History of Robotics
As mentioned in the introductory para, the first modern robot was installed in 1961 by General Motors. The Unimate was a very basic, hydraulically actuated robot arm, noisy in operation. But as the automotive industry was trying to ramp up production, anything that speeded up the process attracted attention and eyeing the potential benefits, many competitors started working on similar products. In 1962, AMF Corporation manufactured the Verstran (derived from Versatile Transfer) cylindrical robot that was quickly adopted by rival Ford. By late 1960s, Japanese companies were competing in the US automotive industry and Kawasaki obtained a licence to manufacture the Unimate in Japan, thus becoming the first Japanese manufacturer. In 1969, inventor Victor Scheinman working at Stanford University developed the Stanford arm, the first all-electric 6-axis articulated robot. In 1975 ASEA, which later became ABB, developed the first electrically driven robot in Europe, which was also the first microprocessor-controlled robot that used Intel’s first chipset. By the late 1970s, several other companies had developed robots dedicated to specific tasks like welding and painting. By the mid-1980s, Yaskawa had launched the Motorman ERC control system in the US, with power to control up to 12 axes. In 1992, FANUC created the first prototype of an intelligent robot. The era of modern industrial robots had begun.
Major Types of Robots Used in Manufacturing
Industrial robots are classified based on mechanical configuration, and as such, there are six major types, viz., articulated robots, Cartesian robots, SCARA robots, delta robots, spherical or polar robots and cylindrical robots. That apart, robots are also classified according to motion control, power supply control and physical characteristics.
- Articulated robot is one of the most common types and resembles a human arm, which is connected to the base with a twisting joint. Movement of the arm depends on the rotary joints ranging from two to ten – the more the number, the more the degrees of freedom. These robots are very precise and flexible, and are heavy duty workhorses used in material handling, foundries, assembly and welding applications.
- Cartesian robots, also called rectilinear or gantry robots, have a rigid rectangular configuration. The linear motion of these robots is delivered by three prismatic joints sliding on three perpendicular axes (X, Y and Z). An attachment of a ‘wrist’ provides rotational movement if needed. These robots are not very expensive and are used in the majority of industrial assembly and other applications.
- SCARA (Selective Compliance Assembly Robot Arm) robots consist of two parallel joints with a two-link arm layout similar to human arms that can extend or retract easily into confined areas. SCARA robots specialize in lateral movements and are mostly used for assembly applications. The SCARA robots can move faster and have easier integration than cylindrical and Cartesian robots.
- Delta robots, also called parallel link robots, consist of three arms connected to universal joints at a common base. The arms only move in the X, Y, and Z direction with no rotation. The positioning can be controlled easily with its arms, facilitating high speed operation. Delta robots are generally used for fast pick-and-place or product transfer applications.
- Spherical robots, also called polar robots, have a twisting joint connecting the arm with the base and a combination of two rotary joints and one linear joint connecting the links. These robots have a spherical work envelope and the axes form a polar coordinate system. These robots sweep a large volume of space, but the access of the arm is restricted within its workspace.
- Cylindrical robots have at least one rotary joint at the base and at least one prismatic joint connecting the links. These robots have a cylindrical workspace with a pivoting shaft and an extendable arm which moves vertically and by sliding. These robots offer vertical and horizontal linear movement along with rotary movement about the vertical axis.
Common Applications and Robotics Integration in Industries
The various types of robots described above have distinct characteristics making them suitable for specific tasks like pick & place, machine tending, material handling, welding of various types, painting, packaging, assembly, etc. In other words, robots can be integrated into routine industrial operations to perform repetitive and tedious operations as also deployed in hazardous environments which is too dangerous for human operators. However, this may call for professional expertise to determine the exact selection of the robot and its accessories, as robots are an expensive investment, and a wrong choice of hardware can cause a serious setback. There are system integrators who analyze the operations of a plant and offer the correct recommendations about the type of robot best suited for a given operation.
Advantages of Robotic Automation
- For countries with the highest robot density – number of robots per 10,000 population – like Singapore, South Korea, Japan and Germany, robots are a necessity to overcome shortage of labour. These are countries with high productivity in manufacturing industries, manufacturing engineering equipment, machinery, electronics, computers and peripherals, white goods, etc., with a high share of exports. Even China is fast catching up in robot deployment even though labour is abundant because it is competing with these countries in productivity.
- If labour is one part of the productivity equation, quality is another. Robots are not only more productive, but they are also highly accurate and consistent. The most efficient human workers need rest, robots do not. The highly automated automobile plants where a car rolls off the assembly lines after every certain minute, are also high on robotic automation. The weld and paint quality that robots provide is impossible for human labour on that scale. Same is the case with white goods and consumer durables.
- Another important advantage of robots is safety. Robots are often deployed in hazardous areas with high temperatures like foundries and furnaces in steel and heavy engineering industries as well as chemical plants, where human labour is exposed to higher risks. Robots take away the drudgery from human workers.
The Future Scope of Robotics in Manufacturing
As Industry 4.0 technologies usher in the era of smart factories and Lights-Out manufacturing, robots will take over more and more jobs, and work with their human counterparts. The entry of collaborative robots has made this co-working environment safe. In the next ten years, more and more people around the world will be working with robots. With programming and installation of robots becoming simpler and intuitive, most workers will be comfortable handling robots, which has so far been the preserve of experts. Collaboration and digitalization are key drivers that will benefit robot implementation. According to the IFR, in future, Artificial Intelligence and Machine Learning tools will further enable robots to learn by trial-and-error or by video demonstration and self-optimize their movements.
Robots will become smarter, more connected, more mobile and more ‘normal’. They will become an ever increasingly familiar sight not only in manufacturing but in our everyday life, from shelf management in the supermarket, to hotel concierge functions and even serving at restaurants.
Conclusion
Digitalization has unleashed the next wave of automation with emerging technologies helping robots to become even more agile and versatile. The Covid-19 pandemic has also brought home the need for more autonomous factory operations in future, and hence the prospects for industrial robots remain excellent. Robotic automation or use of robots in industry has many advantages that lead to increased productivity. But robots are an expensive investment, and the ROI must be justified, so deploying robots must be a carefully considered decision, with guidance from professionals.
For more information or assistance, send us an email at rfq@enwps.com.