Industry 4.0 Automation Revolution and Emerging Technologies: A Complete Guide
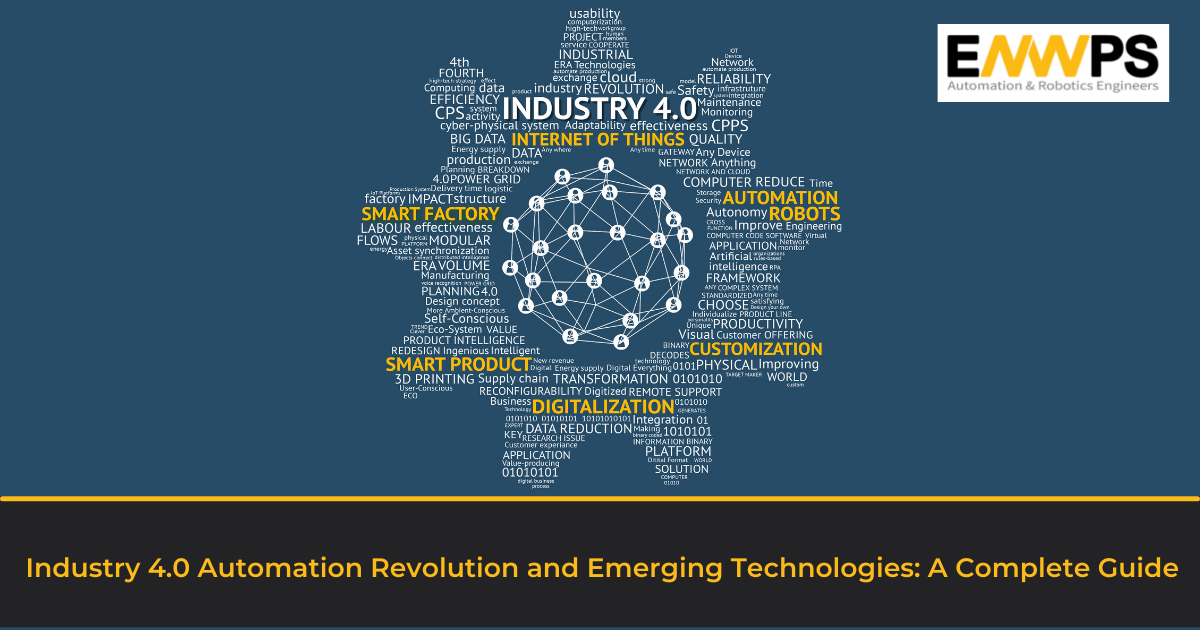
Introduction
The manufacturing industry has undergone a series of revolutionary changes from the first industrial revolution in the 18th century to the present era of Industry 4.0. From the introduction of steam engines in the first industrial revolution to the concept of mass production in the second to the inception of electronics and information technology in the third industrial revolution; the manufacturing industry has seen a paradigm shift at the functional level. In Industry 4.0 the focus has transferred to plant automation, interconnectivity, enhanced human-machine relationships, real-time data, cognitive computing, etc. These digital technologies are paving way for smart manufacturing allowing businesses to leverage data and resources to boost production efficiency, improve decision making, and drive exponential growth. Apart from technological advancements, Industry 4.0 is more about how strategically businesses are integrating these technologies into their existing setup to elevate their profit margins, foster production frequency, and upgrade product quality.
What is Industry 4.0 Automation?
Industry 4.0 automation is a comprehensive term with an emphasis on intelligent networking of machines, processes, and people within an industrial setup to optimize the production through digital technologies like cyber-physical systems, IIoT, cloud computing, robotic automation, etc. These technologies together create a manufacturing system that is equipped with sensors and actuators for remote monitoring, wireless connections for internal communication, robots for automating operations, IoT-enabled industrial systems for improved decision making, data and analytics for enhanced manufacturing efficiency, etc. By thoughtful integration of Industry 4.0 automation, businesses can stay prepared for any changes in demand, processes, or industrial environment contributing to scalability and flexibility of the manufacturing systems. It further opens opportunities for introducing new products by virtualization and helps in the competent management of supply-chains through real-time analytics.
The below comparison shows how Industry 4.0 technologies can impact operations and production efficiency with comparison to traditional practices.
Source: Ronald Berger
Industry 4.0: Technological Advancements
Industry 4.0 does not refer to a single technology. Instead, it is a fusion of several technologies integrated according to automation needs for advanced manufacturing units. It includes:
1. Cyber-Physical Systems: It aims at complete integration of physical processes and devices into a cyber network for the collection of data ensuring optimum security.
2. Autonomous Robots: These are self-reliant intelligent machines that can conclude operations without intervention from human operators.
3. IIoT – Industrial Internet of Things: It refers to the interconnectivity of data and machines for optimizing and automating manufacturing operations.
4. Cloud Computing: It is associated with the use of interconnected remote servers to store, manage, and process information.
5. Big Data and Analytics: The data collected by Cyber-Physical Systems and IIoT, needs to be analyzed and organized for improving decision making and increasing operational efficiency. Thus, Big Data and Analytics help manage and optimize the collected data.
Apart from this, cognitive computing, simulations, augmented reality, additive manufacturing, artificial intelligence, etc. also make up important parts of digital transformation technologies under Industry 4.0.
Real-World Application of Industry 4.0
To help understand how these technologies impact manufacturing ecosystems, below are some of the smart use cases in the real world.
1. Supply-Chain Management: The innovative solutions provided by Industry 4.0 technologies empower businesses with better data visibility, deeper insights, and improved analysis of entire supply chains. It helps eradicate extra costs, reduce lead times, efficiently manage logistics activities, keep a check on inventory levels, and control all the associated tasks. Therefore, optimizing the entire supply-chain process.
2. Asset-Tracking: It refers to identifying and tracking ongoing production processes, machines, human resources, raw materials, etc. By keeping a track of assets, Overall Equipment Effectiveness (OEE) can be strengthened, tactful positioning of equipment and personnel can be done to increase operational efficiency, and ultimately the manufacturing cost of end-product can be reduced.
3. Augmented Reality: Augmented reality involves the use of extra sensory input, for visualizing into existent scenarios. It turns the manufacturing ecosystem into an interactive arena that is capable of quickly identifying problems at initial level and keeping the operations up and running. Augmented reality-enabled devices like- HoloLens’s can be used for employee training, mostly in case of hazard-prone industrial areas.
4. Cobots: We are already aware of autonomous robots used in manufacturing operations for automating industrial processes. However, various manual tasks need human involvement apart from mainstream operations. Cobots are referred to the robots that collaboratively perform manual operations, together with humans. The application of cobots can be found in activities such as quality assurance, material removal, maintenance tasks, etc.
Valuable Outcomes of Industry 4.0 Automation
1. Decentralization of Processes: With help of automated robots, PLCs, SCADA, and HMI systems, the dependency on human operators is reduced allowing machines to make automated decisions based on performance data for managing manufacturing operations.
2. Interoperability: It is associated with the communication ability of computer systems, robots, cyber-physical systems, sensors, and other devices to exchange and make effective use of information. It can help in managing inventory levels, supply chains, detecting errors in operations, etc.
3. Real-time Data Analytics: It includes the use of sensors, IoT devices, etc. that instantaneously feed data and algorithms for quick processing of errors in manufacturing processes, aiding in predictive maintenance, analyzing shop-floor operations, etc.
4. Digital Virtualization: It includes creating virtual simulation models of industrial processes for training, testing, optimizing, etc. without interrupting the plant operations. It’s also beneficial for analyzing the effectiveness of the operations when introducing innovations in the industrial processes.
5. Agility and Flexibility: It allows any production line operation to change instantly according to customer-specific requests without the need to reconfigure the entire assembly line. With help of pre-programmed modules fed into the system, introducing design variations and new models has become extremely easy and quick.
Challenges in Implementation of Industry 4.0 Automation and How to Overcome Them?
With enormous opportunities, Industry 4.0 automation brings in potential challenges that stop business owners from completely incorporating Industry 4.0 technology into their facilities. Some of those challenges are mentioned below:
1. Security: Identity theft, the threat of losing intellectual property, sensitive information about manufacturing processes or client information, etc. are some of the growing concerns among manufacturers. For this purpose, various cybersecurity measures can be adopted on a prior basis for mitigating the involved risks.
2. Availability of Resources and Required Manpower: Industry 4.0 solutions can be easily integrated into a facility’s existing setup while eliminating concerns about available resources. Although Industry 4.0 is a knowledge-intensive technology, with proper training and documentation, industry personnel can easily grasp new changes. Hence, it’s important to look for reliable and supportive service partners when implementing Industry 4.0 solutions.
3. High Costs: One important aspect of automation is that not every process needs to be altered. As all businesses are different and so does their requirements and goals. Hence identifying the processes required to optimize for Industry 4.0 is the key to making efficient use of it. If implemented with a strategic and concrete plan, the costs incurred in implementation can be recovered within a stipulated time. Calculating ROI on a timely basis, checking testability, etc. can save high costs involved in introducing Industry 4.0 into a facility.
Let’s Upgrade Your Industrial Process!
By now, you must have assessed the significance of choosing the right service provider for implementing Industry 4.0 solutions. ENWPS has a two-decade legacy of providing automation and robotics solutions in different industry verticals. From supply, implementation, training, and documentation, our expert team handles all the activities so that our customers can fully rely upon us.
Planning to upgrade your facility? Reach out to us at: rfq@enwps.com for quick assistance. We are looking forward to helping your facility embrace Industry 4.0 automation solutions!